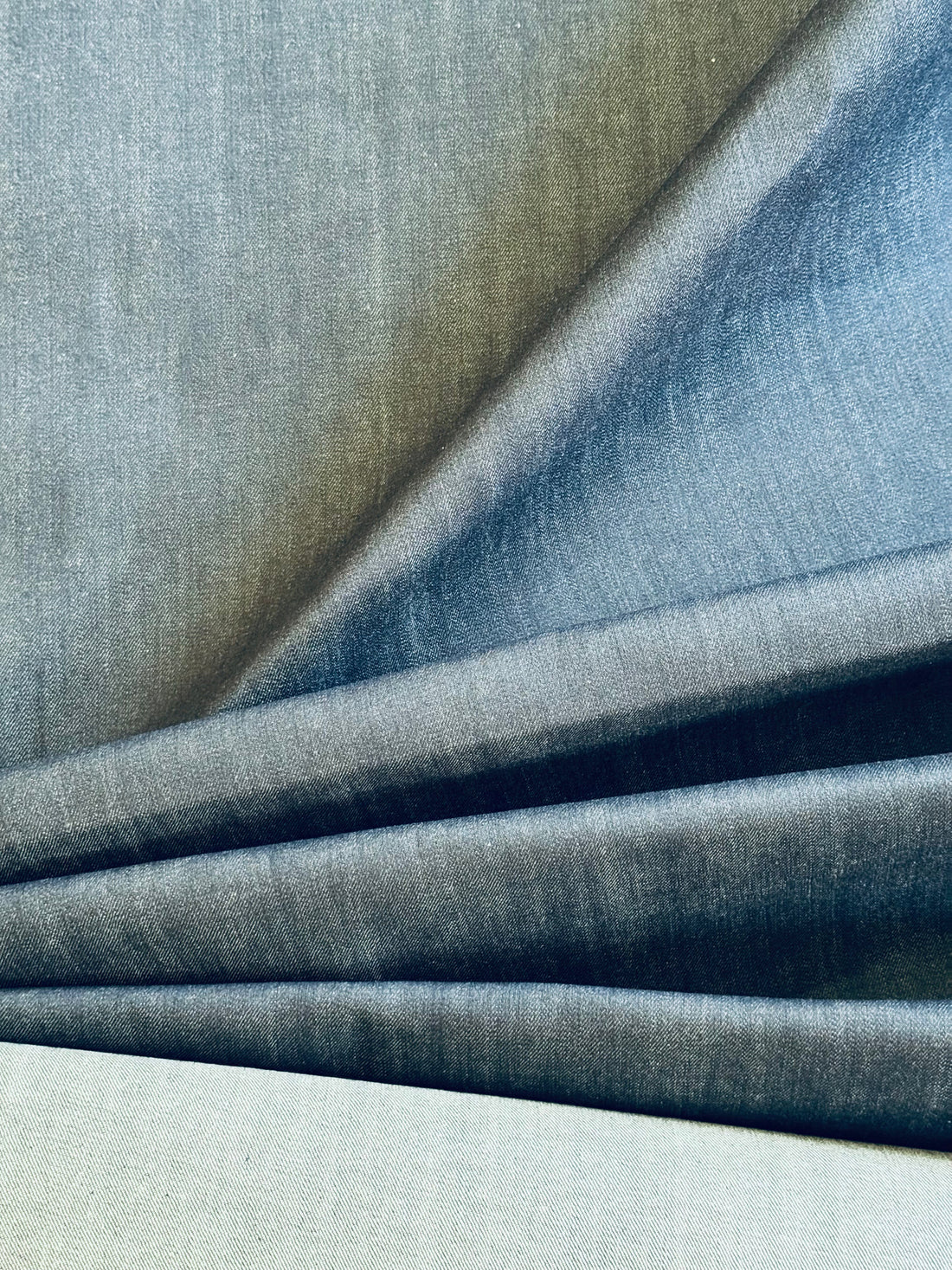
BACK TO BLUE
REVIVING THE LEGACY OF DENIM
By Adriana S. Diaz - January 27, 2025

The fashion industry faces the urgent challenge of reducing its environmental impact. Among the most iconic yet resource-intensive garments, denim holds a special place. "Back to Blue" signifies a call to action—a revival of sustainable denim production practices that honor the past while embracing innovative technologies like 3D modeling and pattern-making.
The Environmental Impact of Denim Products
Denim production, particularly for jeans, demands vast amounts of water, energy, and chemicals, highlighting the environmental toll of denim and the resources involved in creating these garments. Studies show that a single pair of jeans can consume up to 3,800 liters of water throughout its lifecycle, from cotton cultivation to final washes. Additionally, dyeing and finishing processes generate toxic waste that harms local ecosystems.
Addressing these issues is not only an environmental responsibility but also an opportunity to innovate with more efficient and sustainable processes.
Traditional Pattern-Making vs. 3D Pattern-Making

Traditional pattern-making involves creating physical patterns, continuous testing, and adjustments, which consume time and material resources. In contrast, 3D pattern-making digitizes this process, optimizing garment creation and production.
Advantages of 3D Pattern-Making:
- Waste Reduction: Eliminating the need for multiple physical samples minimizes fabric and material waste.
- Precision in Fit: 3D simulations visualize how garments fit various body types and sizes before production.
- Faster Development: Digital pattern creation and adjustment significantly reduce time to market.
Mastering the art of pattern-making for denim with precision ensures perfect fits and durable designs that stand out.
Sustainability in Denim through 3D Modeling

3D modeling takes pattern-making to another level by enabling hyper-realistic visualizations of garments. For denim, this technology is especially valuable, simulating textures, washes, and characteristic distressing. Designers and brands can:
- Reduce Physical Samples: Instead of producing multiple prototypes to adjust cuts or finishes, digital testing lowers material consumption.
- Adopt More Efficient Processes: Simulations help identify design issues before production, reducing errors and rework.
Success Stories in the Denim Industry
Several leading brands are already transforming their denim production processes with 3D modeling:
- Levi's: The brand has adopted digital design to shorten development times and minimize textile waste.
- Tommy Hilfiger: Uses 3D modeling in its collections to visualize denim washes and design details without physical samples.
Additional Benefits for Brands
Beyond environmental advantages, 3D pattern-making offers competitive benefits:
- Enhanced Customer Experience: Brands can showcase their products interactively, allowing customers to customize garments before purchasing.
- Cost Reduction: Reduced reliance on physical samples and faster testing processes lower overall production costs.
Conclusion: A Sustainable Future for Denim
Combining 3D pattern-making and modeling represents a revolution in denim production. By adopting these technologies, brands can significantly reduce their environmental impact, increase efficiency, and connect with a market increasingly aware of sustainability.
"Back to Blue" is more than a return to denim's roots—it’s a leap forward in creating a responsible and innovative future. The mastery of pattern-making ensures precision, perfect fits, and designs that endure the test of time, paving the way for denim to shine once again. Let’s bring denim back to blue.